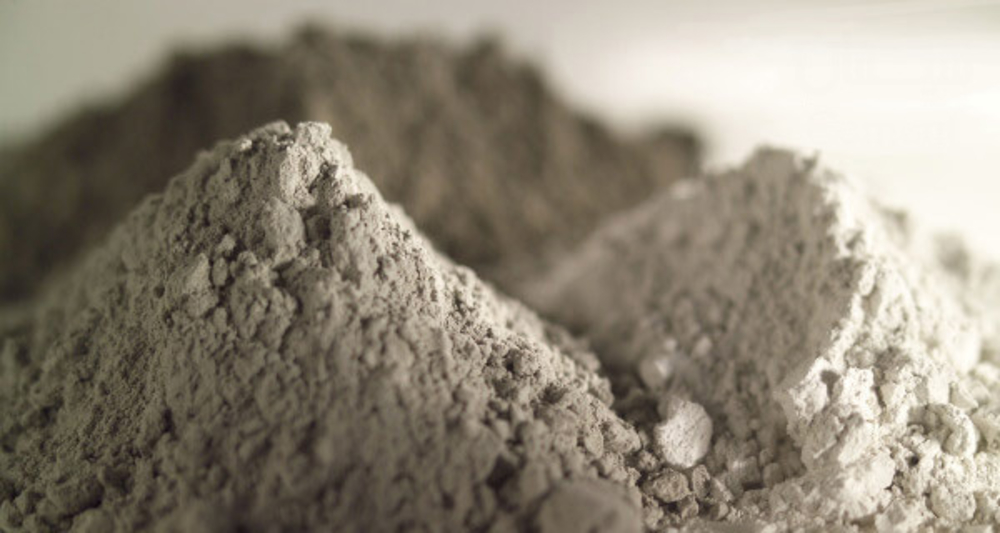
تاریخچه کشف سیمان یا Cement
همه ما بارها نام سیمان یا سمنت را شنیده ایم و یا از آن استفاده کرده ایم اما در این مقاله به تاریخچه کشف سیمان و طرز تهیه آن می پردازیم. سیمان یک ماده هیدرولیکی است که در وهله اول از سوزاندن مخلوط آهک و خاک رس به دست میآید. ماده حاصل از این فرآیند “کلینکر” نام دارد، که بعدا پودر میشود و ترکیبی از خواص شیمیایی و فیزیکی خاص خود را دارد.
سیمان دارای ریشه آهکی می باشد . به عبارت دیگر ماده اصلی تشکیل دهنده آن آهک و ماده اولیه اصلی آن سنگ آهک است.
اولین بار در تاریخ بشر کاری که در زمینه تهیه مخلوط مصنوعی از سنگ آهک و خاک رس برای تهیه سیمان ( آهک آبی ) صورت گرفت ، در کشور فرانسه و توسط ویکات در ابتدای قرن نوزدهم بود . ویکات، سنگ آهک و خاک رس را با هم مخلوط کرد و سپس به همراه آب این مخلوط را آسیاب نمود و دوغاب حاصله را پخت. گرچه نتیجه حاصله موفقیت آمیز بود ،ولی عملا در فرانسه این روش ادامه داده نشده تا اینکه در انگلستان یک بنای آجرچین موفق شد از پختن مخلوطی از سنگ آهک و خاک رس (به نسبت متفاوت و بصورت دوغاب) در درجه حرارت بالا به نوعی آهک آبی فوق العاده جالب دست یابد . وی نام این محصول بدست آمده را سیمان پرتلند گذاشت و در 21 اکتبر 1824 سیمان اختراعی خود را به ثبت رسانید.
قسمت عمده سیمان مصرفی از نوع سیمان پرتلند می باشد. اجازه دهید علت این نامگذاری ( سیمان پرتلند ) را بیشتر توضیح دهیم علت این نامگذاری، این بود که بتن ( سنگ مصنوعی ) حاصل از این آهک آبی و خرده سنگ شباهت های زیادی ( خصوصا از نظر رنگ ) با نوعی سنگ آهک داشت که در جنوب انگلستان و در جزیره پرتلند یافت می شد.
*البته این سیمان با آنچه هم اکنون به نام سیمان پرتلند معروف است تفاوت دارد و کاملا مشابه نیست.
کار اسپیدین توسط پسرش ویلیام پیگیری شد و وی توانست در سال 1843 با دست یابی به تکنیک استفاده از درجات حرارت بالاتر و ایجاد حالت عرق کردن در حین پخت به محصولی دست یابد که درصد قابل توجهی از مواد مورد استفاده به صورت گداخته شده و مابقی به صورت پخته شده درآید. منظور از گداخته شدن همان پختن در درجات حرارت بالاست ، بطوری که بخشی از مواد در حال پخت به صورت گداخته (مذاب) درآیند . سیمان ساخته شده توسط ویلیام اسپیدین واقعا بهتر و عالی تر از سیمان های قبلی بوده و دارای مقاومت بیشتری بود . از این سیمان در ساختمان جدید پارلمان انگلستان (1840_1852) استفاده گردید .
اولین کارخانه سیمان ایران را چه کسی ساخت ؟
مطالعات تاریخی نشان میدهد که ایرانیان نیز همانند فینیقیها و یونانیها و رومیها ، قادر به تهیه ملاتهای آبی بودهاند که توانایی تحمل فشار و انسجام خود را در مجاورت آب نیز حفظ میکرده است ، آثار باقیماندهای مانند سدها و پلهای عظیم در مناطق مختلف ایران همچون سد
ایزدخواست که اولین سد قوسی جهان بهشمار میرود ، سد کرخه و سد شادروان، مسلم میسازد که ایرانیها از دیرباز خواص هیدرولیک آهک را میشناختهاند، حتی پختن آهک را رومیها از یونانیها و یونانیها از ایرانیان فرا گرفتند، زیرا قدیمیترین ملات آهکی در ایران کشف شده است.
نخستین گام برای راهاندازی صنعت سیمان را در ایران، علیقلی خان سپاهی دنبلی ملقب به مهندسالدوله برداشت که در سال ۱۲۹۲ خورشیدی از پلیتکنیک زوریخ فارغالتحصیل شده بود .
او در سال ۱۲۹۵ خورشیدی قراردادى برای کسب امتیاز انحصارى ساخت کارخانه سیمان با وزارت فوائد عامه بست اما چون مجلس شورای ملی تا پنج سال بعد به دلیل شرایط جنگی تعطیل بود امتیازهای انحصاری باید به تصویب مجلس میرسید.
در آن زمان، سیمان ایران از روسیه تأمین و از باکو وارد کشور می شد.
از آغاز قرن چهاردهم خورشیدی رویکرد جدیدی به سوی توسعه اقتصادی و مدرن سازی کشور مد نظر قرار گرفت و به تبع آن طرحهای بسیاری از قبیل خطوط راهآهن، سدها، جادهها، اماکن آموزشی و عمومی متعددی در دستورکار قرارگرفت.
ساخت تأسیسات و ساختمانهای جدید ، استفاده از مصالح جدید را نیز در سرلوحه برنامههای توسعهای قرار میداد که بالطبع سیمان یکی از مهمترین این مصالح بود. توجه به این نکته که ایران در منطقهای واقع شده که سلسله کوههای آهکی آن را احاطه نمودهاست، اندیشه ساخت کارخانه سیمان را پدیدار ساخت. در سال ۱۳۰۷ مطالعات لازم برای ایجاد اولین کارخانه سیمان آغاز گردید و هشتاد و نه سال پیش کارخانه سیمان واقع در بین راه حضرت عبدالعظیم در پای کوه چشمه علی افتتاح شد.
(منصور) وزیر طرق گفت: قسمتی از اولین کارخانه سیمان ایران از دانمارک و بخشی از سوئد خریداری شده است. همچنین این کارخانه روزانه استعداد ساختن ۱۰۰ تن سیمان را دارد در روز ۸ دیماه ۱۳۱۲ اولین کوره سیمان ایران با ظرفیت ۱۰۰ تن در روز در «شرکت سیمان ری» به بهرهبرداری رسید.
کوره های سیمان پزی
انواع کوره های پخت سیمان در کشورهای مختلف وجود دارد اما بسیاری از آن ها در ایران استفاده نمی شوند و رایج نیستند.
کوره های کارخانه سیمان در ایران معمولا کوره گردنده خفته می باشد. از کوره ایستاده در ایران به ندرت استفاده می شود. انواع کوره های سیمان پزی شامل : کوره گردنده خفته، کوره ایستاده و کوره های پیش گرمکن سیمان می باشد که در ادامه به شرح آن ها می پردازیم.
کوره گردنده خفته :
کوره سیمان پزی گردنده، از یک استوانه فلزی به طول 100 متر و قطر 4 متر و ضخامت بدنه 20 تا 40 میلی متر با شیب 3 تا 4 درصد نسبت به افق ساخته شده است که 1/5 تا 2 دور در دقیقه حول محور خود می چرخد. لوله روی پایه هایی قرار داشته و یک موتور چرخ دنده حرکت دورانی آن را تامین میکند.
کوره ایستاده :
کوره پخت سیمان ایستاده از استوانه با قطر 3 متر که دهانه بالای آن گشادتر است و به طول 10 متر تشکیل شده است، مواد سیمان را با رطوبت به شکل گلوله هایی به قطر 10 سانتی متر درآورده، آن را با ذغال کک به کوره می ریزند و کوره را از پایین آتش می کنند. پس از پختن، کلینکر را از زیر آن خارج می کنند. کلینکر در هنگام فرود 1200 درجه سانتی گراد حرارت دارد. سوخت این کوره ها از ذغال، نفت و گاز تامین می شود. کیفیت سیمان ایده آل نیست.
کوره های پیش گرمکن سیمان :
در کوره های پخت سیمان، پیش گرمکن یکی از واحدهای مهم می باشد. در پیش گرمکن، قبل از این که مواد وارد کوره شوند، مواد خام را آماده ریختن به کوره می کند .
سیمان، فرآیند تولید و تکنولوژی آن
مواد اولیه
مواد اولیه مورد استفاده در صنعت سیمان معمولاٌ سنگ آهک و خاك رس است که پس از استخراج بوسیله کامیون (یا در مواردی بوسیله واگن، کشتی، نوار نقاله و… ) به محل کارخانه و به قسمت سنگ شکن حمل میشوند. خاك و سنگ آهک بصورت جداگانه از خرد کن عبور کرده و خرد میگردد. در سنگ شکن که مخصوص خرد کردن سنگهاي تا ابعاد دو متر میباشد، سنگ خرد (شکسته) شده و بستگی به نوع سنگ شکن و آسیاب مواد ابعاد آن به کمتر از 8 سانتیمتر تقلیل مییابد.
سالن مواد
پس از خرد شدن سنگ آهک و آماده شدن خاك، این دو در یک سالن با یکدیگر مخلوط میشوند و یا در دو سالن جداگانه ریخته میشوند و سپس به نسبت لازم قبل از ورود به آسیاب مواد با یکدیگر مخلوط میگردند. ممکن است به مخلوط حاصله مواد اولیه دیگري نظیر سنگ آهن به منظور کمک ذوب یا سنگ سیلیس جهت تصحیح و تنظیم ترکیب شیمیائی مواد براي ساخت سیمان ضد سولفات اضافه شود که این عمل میتواند هم در سالن مواد صورت گیرد و هم اینکه مواد اولیه اصلی در قیفها و سیستم توزین وارد آسیاب مواد شوند.
آسیاب مواد اولیه
آسیاب مواد انواع مختلفی دارد و در خط تولید مورد بحث از نوع گلولهاي میباشد. اصولاٌ در آسیاب مواد، مواد اولیه خرد شده به نسبتهاي لازم وارد آسیاب میشوند و سپس بصورت پودر، با رطوبت کمتر از موقع ورود، از آسیاب خارج میگردند. آنچه که از آسیاب مواد خارج میشود بنام مواد خام یا خوراك کوره نیز موسوم است. آسیاب موادر مجهز به کوره هواي گرم براي گرفتن رطوبت مواد میباشد، غالباً از گازهاي گرم خروجی از کوره براي این منظور استفاده میشود. این کوره براي مواردي است که کوره اصلی متوقف میباشد.
غبارگیری
به منظور خشک کردن و جابجائی مواد در آسیاب مواد از گازهاي خروجی از کوره استفاده می شود. این گازها از انتقال مواد از آسیاب موارد الکترو فیلتر گشته و ذرات مواد و گرد و غبار از آن جدا میگردد و سپس از طریق دود کش به خارج (محیط اطراف) فرستاده میشود.
مواد پودر شده پس از خروج از آسیاب، وارد سیلوهای مخلوط کن و ذخیرهسازي میشود و پس از نمونهگیري و آزمایشات لازمه توسط آزمایشگاه و اطمینان از تنظیم بودن و متناسب بودن ترکیب مواد خام، هموژن میگردد و سپس به سیلوهای ذخیره خوراك فرستاده میشود. در خط تولید مورد بحث فقط یک سیلو از نوع جریان پیوسته به ظرفیت 25000 تن منظور شده است. در این قسمت مواد ذخیره شده آماده مصرف در کوره میباشد.
کوره و پیش گرمکن
مواد خام از قسمت بالاي پیش گرم کن وارد سیستم پخت میشود و پس از عبور پیش گرم کن و کلساینر وارد کوره دوار میگردد. مواد خام در پیش گرم کن به مرور ( در فاصله حدود50 ثانیه) خشک، گرم و کلسینه میشود. پیش گرم کن داراي دو برج است. مواد موجود در سیلوها چه به صورت لجن و چه به صورت پودر دارای حرارت محیط می باشد و اغلب دارای آب فیزیکی هستند که اگر به همین صورت وارد کوره شوند اولاً مصرف سوخت را بالا می برند و ثانیاً در کار پخت سیمان اخلال ایجاد می کنند به همین جهت مواد داخل سیلو قبل از ورود به کوره ی اصلی وارد کوره ی پیش گرم کن می شوند.
قسمت اصلی عمل پختن در کوره صورت می گیرد. کوره سیمان یک استوانه فلزی است که طول و قطر آن متناسب با ظرفیت کارخانه می باشد.
مواد پس از تکلیس وارده کوره شده و نهایتاٌ بصورت دسیمان پرتلند چیستانهاي کلینکر از کوره خارج میگردد. سیستم پخت متشکل از پیش گرمکن، کلساینر، کانال هواي سوم، کوره دوار، خنک کن و دستگاه جداسازي قلیائی (کنارگذر) میباشد.
خنک کن کلینکر
درجه حرارت کلینکر خروجی از کوره حدود 1300 درجه سانتیگراد است و این مقدار حرارت موجود در کلینکر بوسیله جریان هواي سرد بازیابی میشود. سپس کلینکر خنک شده (تا حدود100 درجه سانتیگراد) راهی انبار کلینکر میگردد. بخشی از هواي گرم شده از طریق کانال هواي سوم بسمت کلساینر میرود و بخشی دیگر وارد کوره میشود و اکسیژن مورد نیاز سوخت را تامین میکند.
خرد کن و قیف سنگ گچ
به کلینکر خروجی از کوره حدود 4 درصد سنگ گچ افزوده میشود و سپس در آسیاب سیمان پودر میگردند. قبلاٌ سنگ گچ (گچ خام) در خرد کن جداگانهاي به اندازههاي کمتر از 4 سانتیمتر خرد شده و سپس در قیف مربوطه ذخیره شده است. سرعت ترکیب پودر کلینکر با آب بسیار شدید است و به همین خاطر از سنگ گچ براي کنترل این ترکیب و گیرش سیمان استفاده میشود.
آسیاب سیمان
از طریق دو نوار تغذیه مجهز به سیستم توزین، سنگ گچ خرد شده و کلینکر وارد آسیاب سیمان گلوله ای میشوند و پس از پودر شدن، پودر حاصله (سیمان) از طریق بالابر کاسهاي و هوائی (الواتور و ایرلیفت) به سیلوهای ذخیره سیمان فرستاده میشود. در دهه اخیر استفاده از آسیابهاي غلتکی برای پودر کردن کلینکر و تولید سیمان مرسوم شده است؛ از جمله در پروژههای سیمان تهران و فراز فیروزکوه براي دپارتمان آسیاب سیمان، آسیابهای غلتکی خریداری شده است.
سیلوهای سیمان و بارگیرخانه
با توجه به ظرفیت تولید کارخانه تعدادي سیلوي بتونی جهت ذخیره سیمان در نظر گرفته میشود. سپس سیمان به کمک دستگاههاي بارگیري سیمان فله یا بسته بندي و پر شدن در کیسه ( کیسه پروپیلن) بارگیري شده و از کارخانه صادر میگردد. وسیله حمل سیمان از کارخانه میتواند کامیون، بادسان، تریلی، بونکر، قطار و یا کشتی باشد. چگونگی حمل بستگی به موقعیت کارخانه و محل مصرف دار
انواع سیمان پرتلند
انواع سیمان پرتلند در استاندارد ایران به پیروی از استاندارد ASTM عبارتند از :
تیپ 1ـ سیمان پرتلند معمولی
تیپ 2ـ سیمان پرتلند اصلاح شده .
تیپ3ـ سیمان پرتلند زود سخت شونده .
تیپ 4ـ سیمان پرتلند با حرارت کم .
تیپ 5ـ سیمان پرتلند ضد سولفات .
تجهیزات لازم برای تولید هر پنج نوع سیمان فوق و خط تولید آنها مشابه است و عمده اختلاف در مقدار مواد اولیه و درجه حرارت کوره میباشد.
1- سیمان پرتلند تیپ 1
این نوع سیمان که سیمان پرتلند معمولی نیز نامیده میشود، برای مصارف عمومی که ویژگی خاصی از بتن خواسته نشده است، مصرف میشود. از این نوع سیمان در ساختن پیاده روها، روسازی جاده ها، پلهای بتن مسلح، راه آهن، مخازن، لوله های آب و ملات برای بنایی استفاده میشود. به طور کلی بهتر است از این سیمان در مواردی که نیاز به خواص ویژه دیگر سیمانها علی الخصوص در محیطهای خورنده حاوی یونهای مهاجم بتن استفاده نشود اخیرا سیمان پرتلند معمولی در سه کلاس 325-1 ،425-1 و 525 -1 تولید و عرضه میشود. برای کلاسهای با مقاومت بالا (435-1 و 525 -1) وجود دارد، مصرف این کلاس از سیمان بایستی با احتیاط صورت گیرد. سیمان پرتلند معمولی در کارهای معمولی و عمومی بتنی ساده و بتن آرمه که مکان حمله سولفات ها وجود ندارد مصرف می شود.
2- سیمان پرتلند تیپ 2
از سیمان اصلاح شده در مواردی که حرارت هیدراتاسیون متوسط و مقاومت در برابر حمله سولفاتهای در حد متوسط لازم باشد و از سیمان معمولی مقاوم تر است به کار میرود. به دلیل محدودیت فاز آلومینات و کمتر بودن فاز C3S در این سیمان که سبب ایجاد خواص ویژه مزبور میشود، مقاومت فشاری اولیه و نهایی آن کمتر از سیمان تیپ 1 سیا سیمان پرتلند معمولی است. سیمان تیپ 2 یا سیمان اصلاح شده معمولاً کندتر از سیمان تیپ 1 میگیرد و در گیرش حرارت کمتری تولید میکند. از این سیمان میتوان در ساختمانهای حجیم استفاده نمود تا هنگام گرفتن بتن حرارت کمتری ایجاد شود و حجم بتن ریزی محدود نشود. این سیمان در محیطهای آب و خاک که غلظت یون سولفات در حد متوسط است و برای بتن ریزی در هوای نسبتاً گرم که خطر افزایش دمای بتن معمولی به بیش از 32 درجه سانتیگراد و بتن حجیم به بیش از 15 درجه سانتیگراد وجود دارد، به کار میرود. برای استفاده در محیط های حاوی یون کلر و سولفات به طور همزمان و در محیط های حاوی غلظت زیاد سولفات و همچنین برای بتن ریزی در هوای سرد این نوع سیمان توصیه نمیشود. گرمازدایی این نوع سیمان هنگام آبگیری کمتر از سیمان معمولیست، لذا، در بتن ریزی های حجیم و بتن ریزی در هوای گرم نیز به مصرف می رسد. . در حال حاضر در ایران کارخانه های تولید سیمان مانند سیمان تهران ، سیمان آبیک ، سیمان ساوه ، سیمان شمال ( سیمان جاجرود ) سیمان سبزوار ، سیمان نیزار قم، سیمان جوین و … همگی سیمان پرتلند نوع دو را تولید می کنند.
3- سیمان پرتلند تیپ 3
سیمان تیپ 3 که به سیمان خیلی زودگیر معروف است، این نوع سیمان تقریبا اجزاء اولیه تیپ 1 را دارد، با این تفاوت که به شدت ریزتر آسیاب شده و به همین جهت گیرش سریع تری دارد. سیمان نوع 3 در مدت کوتاهی یعنی معمولا در عرض 1 هفته یا کمتر مقاومت زیادی به دست می آورد و مقاومت 7 روزه آن حدود مقاومت 28 روزه سیمان نوع 1 میباشد. این نوع سیمان نسبت به سیمان نوع 1 در هنگام گیرش حرارت بیشتری تولید میکند. از این سیمان وقتی استفاده میکنند که بخواهند زودتر از معمول قالب را برداشته و بتن را مورد استفاده و بارگذاری قرار دهند. در محیط های سرد نیز میتوان از این سیمان استفاده کرد تا مدت زمان لازم برای محافظت بتن ریخته شده کوتاهتر شود. اگرچه با به کار بردن مخلوط پر سیمان تر با سیمان نوع 1 هم میتوان بتنی تهیه کرد که در مدت کوتاه مقاومت بیشتری کسب کند، ولی سیمان نوع 3 همین کار را به نحو بهتر و با صرفه تر انجام میدهد. سیمان نوع 3 را سیمان زودگیر هم میگویند. در هوای سرد (حدود 4 درجه سانتیگراد)، در دمای زیر صفر درجه سانتیگراد کاربرد این سیمان به تنهایی کفایت نمیکند و لذا در یخبندان علاوه بر مصرف این سیمان مسائل دیگری نیز باید رعایت شود (مثلاً مصرف ضد یخ)؛ سیمان تیپ 3 در ساعات اولیه مصرف، حرارت قابل توجهی آزاد میکند و باعث گرم شدن بتن میشود. این نوع سیمان را در مواقعی که بارگذاری باید مدتی کوتاه بعد از بتن ریزی صورت گیرد یا بخواهند قالب ها را زودتر بردارند یا به هنگام بتن ریزی در هوای سرد به مصرف می رسانند.
4- سیمان پرتلند تیپ 4
سیمان تیپ 4 کندگیر بوده و در هنگام بتن ریزی حرارت کمتری تولید میکند. مقدار C3A و C3S موجود در این نوع سیمان در مقایسه با C انواع دیگر سیمان، کمتر بوده و در مقابل C2S زیادتری دارد. مورد استفاده این نوع سیمان جایی است که شدت و مقدار حرارت تولید شده اهمیت دارد. بتنی که با این سیمان ساخته میشود، رشد مقاومت آهسته تری دارد؛ یعنی دیرتر می گیرد. کاربرد اصلی این نوع سیمان در ساختمانهای حجیم بتنی است. در ساختمانهای حجیم چون سدهای وزنی بتنی به علت حجم زیاد بتن، افزایش درجه حرارت ناشی از گیرش بتن می تواند بسیار خطرناک باشد. برای پایین نگه داشتن درجه حرارت سیمان، سیمان نوع 4 که به آن سیمان دیرگیر نیز میگویند استفاده میشود. این نوع سیمان در هوای گرم و دمای بالای 40 الی 50 درجه سانتیگراد برای تسهیل مراقبت از بتن به کار میرود. مصرف این نوع سیمان در هوای گرم باعث جلوگیری از اتصال سرد میشود؛ چرا که در بتن ریزی دیوارها (دیوار مخزن آب و یا استخر) که طول دیوار زیاد است، چون بتن ریزی لایه لایه انجام می گیرد، ممکن است فاصله زمانی حدود نیم ساعت یا بیشتر طول بکشد تا لایه بتن جدید روی بتن قبلی ریخته شود. بدین ترتیب در هنگام ریختن بتن لایه جدید، بتن لایه قبلی سفت شده و اتصال خوبی بین دو لایه برقرار نمیشود. این اتصال ضعیف بین لایه های بتن قدیم و جدید را اتصال سرد میگویند که ضعف بتن ریزی به شمار میرود. به خصوص اگر سازه آبی باشد این اتصال نقطه ضعفی برای نشت آب خواهد بود. مصرف سیمان تیپ چهار در چنین مواردی باعث میشود که فرصت کافی برای بتن ریزی فراهم باشد و لایه های قبلی هنوز وارد واکنش نشده باشند تا بتوانند با لایه های جدید اتصال مناسبی را برقرار نمایند. در بتن ریزیهای حجیم به منظور کاهش تنشهای حرارتی میتوان از این سیمان استفاده کرد. بتن حجیم بتنی را گویند که طول و عرض و ارتفاع آن زیاد باشد؛ مانند بتن ریزی سدها و یا پایه های پل. از اشکالات بتن ریزی حجیم، ایجاد تنشهای حرارتی است بدین صورت که به دلیل حجیم بودن بتن، تبادل حرارتی عمق بتن با محیط بیرونی، کندتر صورت میگیرد. بنابراین هنگامی که بتن سفت شد، هنوز دمای قسمتهای مرکزی آن با محیط اطراف، یکنواخت نشده است. از این لحظه به بعد تغییر دمای بتن در راستای تبادل حرارتی با محیط خارج، همراه با ایجاد تنشهای حرارتی خواهد بود. استفاده از سیمان تیپ 4 سبب میشود که اولا دمای قسمتهای میانی بتن حجیم کمتر از بتن مشابه ساخته شده با سیمان تیپ 1 باشد (چون سیمان تیپ 4 هم کم حرارت تر است و هم دمای خود را در طول زمان بیشتری آزاد میکند) و ثانیاً فرآیند سفت شدن بتن طولانی تر بوده و در این مدت قسمت اعظمی از تبادل حرارتی با محیط اطراف صورت می پذیرد. البته اگر خطر کاهش دمای بتن به کمتر از 5 درجه سانتیگراد وجود دارد، بهتر است از سیمان نوع 4 برای بتن ریزی استفاده نشود. این نوع سیمان غالبا در بتن ریزی های حجیم به ویژه در فصول گرم به مصرف می رسد. جهت خرید و اطلاع از قیمت انواع سیمان پرتلند می توانید با مشاوران و کارشناسان فنی و تخصصی دیجی مصالح در ارتباط باشید.
5- سیمان پرتلند تیپ 5
ین سیمان برای مصرف در بتن ها و در بخش هایی از ساختمان که شدیدا در معرض حمله سولفاتها قرار دارد، مناسب است و به همین جهت به سیمان ضد سولفات شهرت دارد. این نوع سیمان وقتی به کار میرود که بتن در تماس شدید با سولفات قرار داشته باشد. از این سیمان اساساً وقتی استفاده میشود که خاک یا آب زیرزمینی که در تماس با ساختمان بتنی قرار دارد، مقدار زیادی املاح سولفات داشته باشد. طبق آیین نامه بتن ایران (آبا) کلیه سازه های بتنی قرار گرفته در محیطهای آب و خاک سولفاتی شدید بایستی از سیمان نوع 5 استفاده شود. البته اگر در محیط یون کلر همراه یون سولفات باشد، کاربرد این سیمان باید با احتیاط و با آزمایشهای لازم صورت گیرد سیمان نوع 5 دیرتر از سیمان معمولی میگیرد و حد مقاومت 3 ،7 و 28 روزه برای این سیمان کمتر از سایر سیمانهای پرتلند است و لذا برای سازه هایی که نیاز به مقاومتهای زیادتر یا مقاوم سازی سازه های بتنی باشد، دارای محدودیت کاربرد است. کارخانه های سیمان تهران، سیمان درود، سیمان اصفهان، سیمان دلیجان، سیمان شرق مشهد و … خط تولید سیمان نوع پنج را دارا می باشند.
انواع دیگر سیمان
سیمان سفید
سیمان سفید را نوعی سیمان پرتلند ویژه که پس از استفاده به رنگ شیری یا برفی ظاهر می شود، تعریف کرده اند.
سیمان سفید از آهک خالص (گچ) و رس ساخته شده است که کاملا خالی از اکسید آهن و هر رنگدانه دیگری مانند منگنز و کروم است. مقاومت و زمان گیرش سیمان سفید همانند سیمان پرتلند معمولی است. رنگ تیره سیمان به دلیل وجود سولفات آهن و سولفات منیزیم در سیمان است. همچنین دوده ناشی از سوخت نیز باعث رنگ تیره سیمان می شود. پس برای سفید شدن سیمان باید سولفات آهن و منیزیم از سیمان حذف شود و هم چنین از سوخت مناسب و بدون دوده استفاده شود.
از سیمان سفید برای ساخت موانع بزرگراه ها، نمای ساختمان، برای اهداف تزئینی و … استفاده می شود، همچنین به طور گسترده ای برای ساخت سنگ های ریخته گری جذاب مورد استفاده قرار می گیرند.
این نوع سیمان نسبتا از سیمان عادی گران تر بوده بنابراین در موارد خاص به کار گرفته می شود.
کار خانه های سیمان سفید ساوه ، سیمان سفید بنوید ، سیمان سفید تهران ، سیمان سفید نیریز ، سیمان سفید کرمان ، سیمان سفید شرق مشهد و … در حال حاضر سیمان سفید را در بسته بندی های 25 کیلویی، 40 کیلویی و 50 کیلویی در بازار عرضه می کنند. سیمان سفید فله نیز توسط بونکر های حمل سیمان از کارخانه بارگیری و ارسال می شوند.
سیمان رنگی
در این نوع سیمان، رنگ و سیمان پرتلند معمولی در نسبت های مشخص با یکدیگر ترکیب می شوند. رنگ به کار رفته در این سیمان به صورت پودری و ریزدانه است. اغلب از نسبت وزنی کمتر از ۱۰ درصد رنگ در ساخت این نوع سیمان استفاده می شود.
- اکسید کروم برای رنگ سبز
- کبالت برای رنگ آبی
- آهن اکسید برای سایه رنگ های قرمز، قهوه ای و زرد.
- منگنز دی اکسید برای ایجاد رنگ مشکی و قهوه ای تیره.
از این نوع سیمان برای پوشش کف و اهداف تزئینی در ساختمان سازی استفاده می شود.
سیمان پوزولانی
این سیمان از مخلوط کردن 15 الی 40 درصد پوزولان با کلینکر سیمان معمولی و آسیاب کردن این مخلوط به دست می آورند. در ایران معادن پوزولان زیادی وجود دارد که می توان از آن ها در تولید این سیمان استفاده کرد. جنس پوزولان سیلیکات و تقریباً شبیه سیمان است، منتهی واکنش های مشخص سیمان را ندارد و خاصیت چسبندگی نیز ندار. سیمان پوزولانی دارای خواص مشابهی با سیمان عادی است اما ویژگی های دیگری نیز در این نوع سیمان مشاهده می شود.
- تولید حرارت پایین.
- مقاومت بیشتر در برابر سولفات ها و خوردگی در برابر آب دریا.
این ویژگی ها باعث می شود تا از این نوع سیمان کاربرد بیشتری در نواحی نزدیک ساحل و خاک های سولفاتی پیدا کند. همچنین برای فاضلاب شهری و ساخت و ساز زیر سطح دریا استفاده از سیمان پوزولانی کاربرد دارد.
سیمان چاه نفت
این تیپ سیمان برای استفاده در عمق های ۰ تا ۶۰۰۰ فوت و یا دما های زیر ۱۷۰ فارنهایت مناسب است. و در مواردی به کار می رود که از سنگ سیمان خواص ویژه ای مورد نظر نباشد . سیمان چاه نفت ( سیمان حفاری ) را با افزودن بعضی مواد شیمیایی خاص به کلینکر سیمان معمولی به دست می آورند. این سیمان برای درزگیری چاههای نفت به کار می رود. این نوع سیمان ها دیرگیر بوده و در برابر دما و فشار بالا مقاوم است. سیمان چاه نفت ممکن است در حفر چاههای آب و فاضلاب نیز به مصرف برسد.
کاربرد های سیمان
موارد زیر ازجمله کاربردهای مهم سیمان در کارهای ساختمانی محسوب میشوند :
-
-
- تهیه ملات سیمان
- آمادهسازی بتن
- ساخت سازههای مقاوم در برابر آتش و گرما
- ساخت سازههای مقاوم در برابر فشار آب و سرما
- ساخت سازههای مقاوم در برابر مواد شیمیایی
- تهیه دوغاب
- ساخت جادههای بتنی
- ساخت قطعههای پیشساخته بتنی ( ساخت لولههای سیمانی، بلوک سیمانی و … )
- کاربردهای تزئینی
-
کلام پایانی
انواع سیمان ساختمانی را میتوان از پرکاربردترین مصالح ساختمانی دانست؛ این ماده پرکاربرد در شاتکریت و سیمان پاشی به کمک ساختمان سازان میاید. به همین دلیل هم که قیمت سیمان در هزینههای ساخت ساختمان تاثیر زیادی دارد.